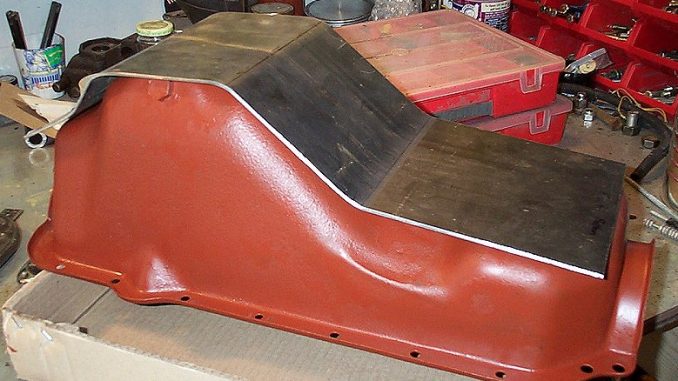
This relatively simply oil pan modification, though it’s being done on Project CJ-7, can be installed on almost ANY 4×4 with an exposed oil pan. Though it may be a rare event to poke a hole in your oil pan, it can happen. At the very least it offers protection from rocks that might chip away the paint and can lead to rust down the road.
Although this Project CJ-7’s engine is a very young crate 360 (approx 14k on it), the parts bolted onto the engine were most likely off of the original Jeep Grand Cherokee. One of the last things that needed attention on the engine was the oil pan. Because it was easier to remove it while it on the frame, I waited until the engine was in before dropping the pan. My main concern was that the visible rust may have eaten too much metal off the pan to salvage it. Once I dropped it off and cleaned it up it turned out not to be too bad. Mostly pitted surface rust. Nothing that some Corroless couldn’t neutralize.
Special note on Coroless Rust Inhibitor…
Since the writing of this page, Corroless is now marketed as a product called Eastwood Rust Encapsulator. Same product, same distributor, different name.
So first thing was to wire-wheel the outside pretty good and wash it down with Simple Green to prep it for paint.
Secondly I made sure the bolt holes were on an even plain. What mean by that is this: when a leak is detected in the oil pan, what the first thing guys do? Tighten the bolt down right? Over time the bolt holes in the pan become recessed due to tightening them down too tight, one too many times. To get a good seal you need to have a flat contact area across the entire seal. So with a small hammer I flattened the holes that appeared to have been tightened down too hard.
With it clean and in good shape, it got a coat of Corroless Rust inhibitor.
Protection for the Vitals
I pondered how I could install a skid plate to protect probably the most important spot on the Jeep, it’s oil pan. One good whack of a sharp rock and I could loose the life blood of the engine. Not good. So coming up with a Skid Plate was a very good idea.
There really is no good way to bolt up a skid plate but a better idea was to attach one to the pan itself. I thought about welding it to it. But I thought a whack to the skid plate might rip the weld and create a hole anyway. Plus welding thin steel is hard without burning a hole in it. Then I thought of a idea that could possibly work even better using some of the best stuff around. Silicone. Why not simply glue the skid plate on with Silicone. Having used it in the past in construction applications I know silicone has tremendous surface tension and using it as a glue would work well.
So I set off to create a skid plate that would not just cover the lowest part of the oil pan but the entire underside of the oil pan. I got the width of the pan plus the totaled length of pan running across the flat areas from front to back.
Using 14 gauge steel, I cut the rectangle, then bent it to conform to the shape of the pan as close as possible. I bent it by creating a make-shift “bending brake” with angle iron and C-clamps (see picture below). To form around the drain plug, I used a small 5 pound sledge to create a relief bend around the plug large enough to fit a socket over the drain plug (see pictures below).
Angle iron c-clamped on the stock for leverage.
How the bends were made in the skid plate:
Forming the drain plug relief bend in the skid plate:
Test for clearance of a socket:
Test fit:
A bend was made too sharp, so to flatten out the bend a little I used a section of railroad rail as an anvil and a sledge to flatten it out:
Next step, I oozed out about an entire tube of GE 50 year Silicone across the areas where the pan metal will meet the skid metal (see picture). Electrical tape was placed over the drain plug to keep it clean of silicone. Then the silicone was worked onto the surface so it covered the whole area it was supposed to cover, not just where it when on from the tube. This increases the surface tension and will help it to “stick” to the oil pan very well.
Then the skid plate was pressed into the silicone and excess was used to cover the sides. Then additional silicone was put on the sides to actually add more protection to the oil pans exposed sides. This should act as a protective cover to deflect rocks and prevent chips and rust down the road as well as possible preventing direct damage.
With adequate time to dry the oil pan was then re-installed with new seals and sealant as well as stainless steel hardware.
Once dry, it would be VERY hard to remove this skid plate even if you were using tools. Don’t under-estimate the holding power of a two foot square area of silicone sealant. A side benefit of using silicone is that if the skid plate ever took a whack, silicone will flex and absorb the shock of an impact. Over all this skid plate cost only about 20 bucks and that includes buying a new gasket for the skid plate. Minus the gasket and it’s really just the cost of paint and the silicone. That’s about six bucks at Walmart providing you have a source for free scrap metal. You can’t beat that for insurance on a vital organ of your vehicle.
What ever happened with this skidplate? Did it work out okay in the long run?
The skid plate worked out great in the long run. After about 10 years of offroad abuse, aside from a layer of dirt and mud, the skid plate looked nearly as good as it did the day it was installed. There are a bunch of nicks in the paint of the skid plate that may have been from contact with kicked-up rocks but that’s about it. EVen the silicone on the sides is intact and still strong as ever. No signs of rust or separation anywhere.