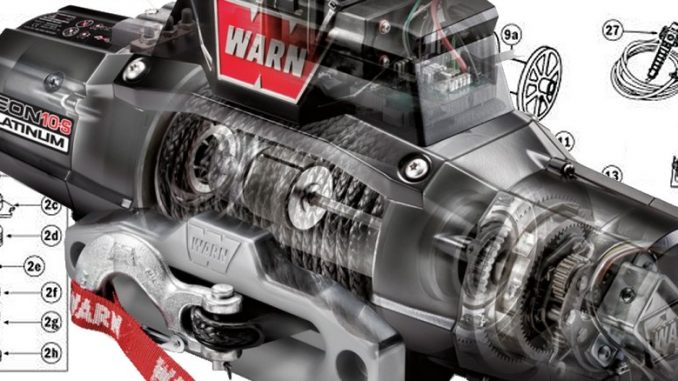
When you look at fundamental differences in common electric winches, a few important components and design characteristics stand out. Of the differences in common winches, the motor and the gear train are the top two design differences that will determine the quality and stamina for an intended use. The motor will vary in motor type and in the horsepower rating. The gear train will vary with different types of gear systems, each with their own characteristics and benefits. Both the motor and gear train work together resulting in the final rating of an electric winch. Understanding these important fundamentals will help you understand what winch you should buy.
Winch Motor Type
Winches use two types of DC motors, Permanent Magnet Motors and Series Wound Motors. All electric DC winch motors consist of one set of coils, called an armature, inside another set of coils or a set of permanent magnets, called the stator. It is the job of the stator to produce a magnetic field which will cause the rotor (or armature) to rotate when an electric current flows through it. Applying a voltage to the coils produces a torque in the armature, resulting in motion. With all types of motors, the higher the horsepower rating, the more toque and power the motor will have. The winch rating is a combination of motor torque and gear train gear ratio reduction. Motor horsepower has a direct effect on both line speed & pulling power.
Permanent Magnet Motors
In a permanent magnet motor, the stator uses permanent magnets and there are no field coils. With permanent magnet motors, the drain on your battery tends to be less than series wound motors, which uses field coils in the stator rather than magnets. Permanent magnet motors are better suited for light to medium duty winching because they tend to generate more heat and overheat. Winching time & load should be carefully monitored as they have the tendency to overheat. The magnets in permanent magnet motors can loose their field strength over time and repeated use.
Series Wound Motors
With a series wound motor, the field coils are connected in series with the armature coil. Series wound motors are powerful and efficient at high speed and generate the most torque for a given current. A series wound motor will uses more current over a permanent magnet motor because they use field coils to generate a magnetic field. Series wound winches are heavier duty winches, and tend to be more expensive.
A permanent magnetic motor will pull the same as a series wound motor, at at less of an amperage draw on the battery and charging system. However, as the permanent magnet motor gets warmer, the power will drop as the amperage draw will increase. The amperage draw on a series wound motor will stay the same throughout the duty cycle.
Winch Ratings
Most winch ratings are generally limited by the maximum amperage draw, with right around 400 being the cut-off point. Anymore than that would most likely damage the power source or charging system. In order to reduce the amperage usually the gear ratio will need to be increased numerically, to relive the motor from the increasing stress, however, this will also reduce the line speed at the same time.
Winch Gear Train – Gear Systems and Spool Diameter
There are three common gearing systems, planetary gear, worm gear, and spur gear. The job of the gear system on all three types is to gear down the high speed motor to a low speed, high torque output to turn the winch drum. The gear reduction ratio is how much the motor’s output revolutions are reduced for the spindle. The greater the reduction, the more revolutions the motor has to turn for one spindle revolution and the less the motor has to work for that revolution. The difference in the gearing systems is mainly in their transfer efficiency.
Planetary Gears
Planetary gears are the most common and provide both strength and smooth operation with good resistance to torque loads. The planetary gear systems have efficiency 65% and have a tendency to free spool when loaded, therefore a braking mechanism is needed.
Worm Gear
The worm gear has a transfer efficiency of 35-40%. This causes the winch to be self-braking even under heavy loads, but this means the unit will need a clutch mechanism for free spooling. Worm gears offer the most reduction, very high reliability, built-in braking mechanism, and generally a slower winching speed. Worm drives are generally stronger and simpler than other gear systems such as the planetary due to the lack of the need for a braking system as well as the extreme gear reductions possible. The primary drawback of a worm gear system is the noticeable reduction in overall line speed, especially in a ‘no load’ cable reel-up situation. Here, the planetary has an advantage.
Spur Gear
The spur gear systems have efficiency of 75% and like the planetary gear system, they have a tendency to free spool when loaded, therefore a braking mechanism is needed. Only the WARN M8274 has a spur gear due to its different design characteristics.
Winch Spool Diameter
The Drum diameter & Gear Ratio have a direct effect on pulling power while affecting line speed at the same time. The width of the drum determines the inevitable loss of pulling power as the cable spools in. As the layers on the drum increase, the effective gear ratio drops reducing the pulling power. The narrower the drum, the quicker the cable spools up and therefore, looses it’s pulling power quicker as compared to a wider drum.
Typical Drum Layered Power Loss
12,000 lbs. Winch Example
Layers Of Cable | Available Pull Power | |
(Bare) 1 | 12,000 lbs. | |
2 | 9,480 lbs. | |
3 | 7,800 lbs. | |
4 | 6,720 lbs. | |
5 | 5,760 lbs. | |
(Full) 6 | 5,160 lbs. |
Winch Solenoid
What is the Solenoid?
Solenoids are electromagnetic switches. When electricity is sent to the solenoid via the remote switch, a magnetic field forms causing the circuit to the winch to complete and the winch motor to move either forward or backward depending on which solenoids are activated.
Solenoid Mounting
Solenoid mounting can be a major consideration. Winches can either have an Integrated or Remote Solenoid pack. A remote solenoid is externally mounted off of the winch. An integrated solenoid is part of the winch either within a “bridge” over the cable or mounted else where on the winch such as above the motor. There are benefits to both types of solenoid mounting options. With space restrictions a remote solenoid can reduce the space require to mount the winch itself while the solenoid can be mounted remotely while an integrated solenoid offers protection in a compact package.
2 or 4 Solenoids?
Some winches have two solenoids, and others have four. Two solenoids configurations are typically found in permanent magnet motor winches and are cheaper, less powerful, heavier, less reliable. Four solenoid configurations are typically found in series wound winches and are stronger, lighter, more reliable.
What are the different “H” numbers of the Winch motor? I think they relate to the operating time/rest time.
Very informative article. Helped me a lot. I want to know how to check winch solenoid…Have you any plan to write about this topic?
Mack, there is a paragraph explaining how to troubleshoot a winch solenoid on this page:
http://www.offroaders.com/winch-tech/winch-troubleshooting/